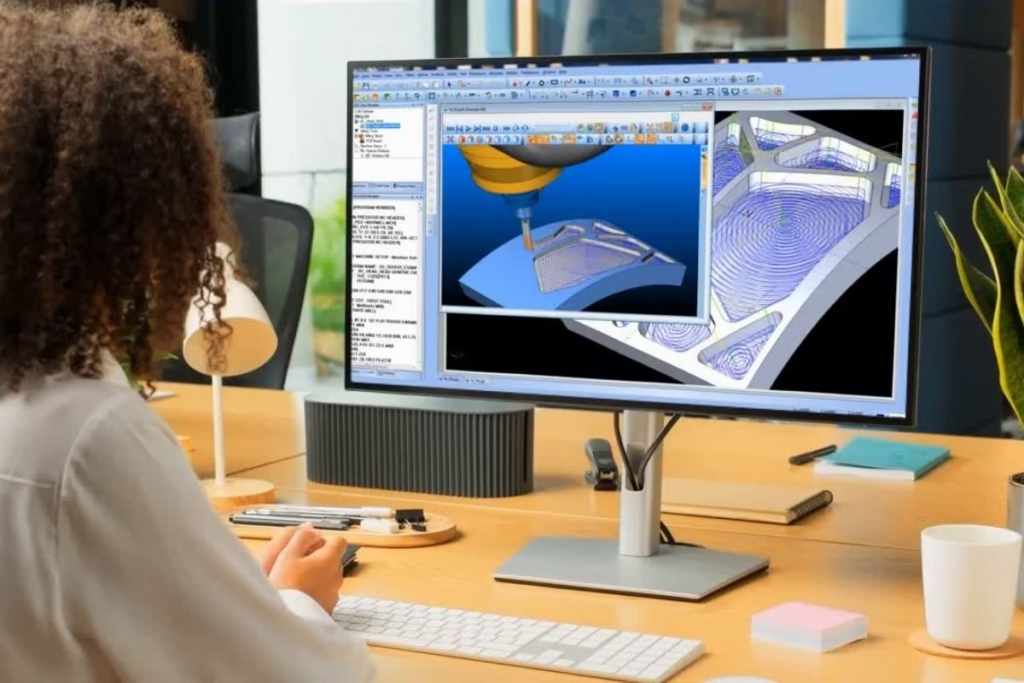
CNC (Computer Numerical Control) programming involves writing instructions, often in the form of G-code, to control the movements and functions of a CNC machine. This allows the machine to automatically process materials, producing parts with precision and efficiency. The programming process typically begins with a CAD model of the desired part, which is then translated into a set of instructions for the CNC machine using CAM (Computer-Aided Manufacturing) software.
Here’s a more detailed look at CNC programming:
1. What it is:
- CNC programming is the process of creating a sequence of instructions that a CNC machine can follow to perform machining operations.
- These instructions, often written in G-code, tell the machine what to do, such as move the cutting tool, set the spindle speed, or change the tool.
- The G-code is essentially a language that the CNC machine understands, allowing it to execute the desired machining process.
2. How it works:
- Design:The process starts with a 3D CAD model of the part to be manufactured.
- CAM Software:A CAM software package is used to analyze the CAD model and generate the tool paths and other instructions for the CNC machine.
- G-code Generation:The CAM software translates the tool paths and other parameters into G-code, which is a sequence of instructions that the CNC machine can understand.
- Programming:The G-code is then loaded into the CNC machine’s control unit, which interprets and executes the instructions.
- Machining:The CNC machine, guided by the G-code, performs the necessary machining operations, such as cutting, milling, or drilling, to produce the finished part.
3. Types of CNC Programming:
- Manual Programming:The programmer directly enters G-code commands into the CNC machine’s control unit.
- Conversational Programming:The programmer uses a simplified, question-and-answer format to guide the CNC machine’s operations.
- CAM Programming:The programmer uses CAD/CAM software to generate G-code automatically from a 3D model.
4. G-code and M-code:
- G-code:Used to control the position of the tool and the workpiece, specifying movements, speeds, and other parameters.
- M-code:Used for miscellaneous functions, such as turning the spindle on or off, changing tools, or controlling coolant flow.
5. Benefits of CNC Programming:
- Automation:CNC programming automates the machining process, reducing the need for manual intervention.
- Precision:CNC machines can perform operations with high precision and accuracy, ensuring consistent part quality.
- Efficiency:CNC programming allows for efficient use of machine time, reducing downtime and increasing production output.
- Cost-effectiveness:CNC programming can lead to cost savings by reducing material waste and improving manufacturing efficiency.
- Flexibility:CNC machines can be programmed to produce a wide variety of parts, making them versatile for different manufacturing applications.
6. Key Concepts in CNC Programming:
- Toolpaths: The paths that the cutting tool follows while machining the part.
- Feed Rates: The speed at which the tool moves across the workpiece.
- Spindle Speeds: The rotational speed of the cutting tool.
- Tool Changes: The process of changing cutting tools during the machining process.
- Coordinates: The points in space that define the tool’s position.
7. Learning CNC Programming:
- Learning CNC programming requires understanding G-code syntax and the principles of CNC machine operation.
- Formal training programs and online resources can provide guidance for learning the basics of CNC programming.
- Practice and hands-on experience are essential for developing proficiency in CNC programming.
In essence, CNC programming is a powerful tool that enables manufacturers to create intricate and precise parts with automation and efficiency, making it a vital skill in today’s manufacturing industry.
Discover more from CNC Toolpath
Subscribe to get the latest posts sent to your email.